ピッキングミスが多い人のため防止テクニック5選
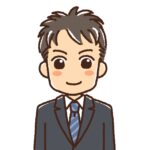
ピッキングかぁ……見るからにキツいってイメージがあるんだけど
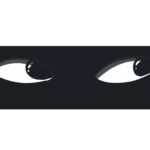
知人に聞いた話だと、やはりキツイらしいぞ
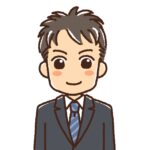
キツいのは体力的に? それとも精神的に?
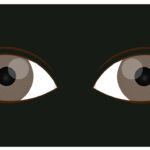
知人の話では、両方だな。
もうやりたくない、と言っていたからな。
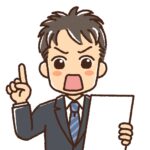
でもこういうキツい作業を誰かがこなしてくれないと、物流が滞っちゃうからね
ピッキング作業は、物流や倉庫業務において非常に重要な役割を果たしています。
商品の保管から出荷までの過程で、ピッキングは顧客のニーズに応えるための最初のステップです。
正確なピッキングがなければ、誤った商品が出荷されてしまい、顧客満足度を大きく損なうことになります。
したがって、ピッキング作業の質は、企業の信頼性や競争力にも直結します。
また、ピッキング作業は効率性にも大きく影響します。
作業がスムーズに進まなければ、納期遅延や在庫管理の不備、さらにはコストの増加を招く可能性があります。
特に、現代のビジネス環境では迅速な対応が求められるため、効果的なピッキング作業の実施が不可欠です。
これにより業務全体のパフォーマンスが向上し、結果的に企業の利益を増加させる事ができるのです。
ピッキング作業は従業員のモチベーションにも影響を与えます。
ミスが多い作業環境では、ストレスや不満が蓄積し、従業員の生産性が低下してしまいます。
逆に効率的なピッキングプロセスが確立されれば、従業員は自信を持って作業に取り組むことができ、チーム全体の士気も高まります。
このように、ピッキング作業の重要性は多岐にわたるため、適切な対策を講じることが求められます。
ピッキング作業においては、さまざまなミスが発生しますが、一般的なミスとして最も多いのは、誤った商品を選んでしまう「誤ピッキング」。
このミスは、特に同じような商品が多くある場合に発生しやすく、結果として顧客に誤った商品が届いてしまうことになります。
これは顧客満足度を低下させるだけでなく、返品処理や再出荷にかかるコストも増加させてしまいます。
次に見られるのが「数量ミス」。
商品をピッキングする際に、必要な数量を誤ってピックしてしまうことがあります。
これにより、在庫が不足したり、過剰に在庫を抱えてしまう結果となります。
在庫管理の不備は、コストの無駄を生むだけでなく、業務の流れを滞らせる要因にもなります。
さらに、作業環境に起因する「作業エラー」も見逃せません。
例えば、倉庫内が混雑していたり、照明が不十分であったりすると、従業員は正確な判断を下すことが難しくなります。
このような状況では、注意力が散漫になり、ミスが発生しやすくなります。
したがって、ピッキング作業におけるミスを防ぐためには、これらの要因を理解し、対策を講じることが重要です。
ピッキングミス防止テクニックその1 適切な在庫管理
適切な在庫管理は、ピッキング作業におけるミスを防ぐための基本的かつ重要なテクニックです。
まず、在庫の正確な把握が不可欠です。倉庫内の商品の数量や位置をリアルタイムで把握できるシステムを導入することで、誤ピッキングや数量ミスを大幅に減少させることができます。
バーコードリーダーやRFID技術を活用することで、在庫情報を迅速かつ正確に取得し、管理することが可能になります。
次に、在庫の配置も重要な要素となります。
よく出荷される商品を倉庫のアクセスしやすい場所に配置することで、ピッキング作業の効率を向上させることができます。
逆に、滅多に出荷されない商品を奥の方に配置することで、作業の流れをスムーズにし、従業員の負担を軽減することができます。
さらに、定期的な在庫の棚卸しを行うことで、在庫情報の正確性を保つことができます。
在庫の状態を定期的に確認し、誤差が生じている場合は即座に対処することで、ミスを未然に防ぐことが可能です。
在庫管理は単なる数字の管理ではなく、効率的なピッキング作業の基盤を築くために欠かせない要素です。
ピッキングミス防止テクニックその2 作業効率化のためのトレーニング
ピッキング作業におけるミスを防ぐためには、従業員への適切なトレーニングが不可欠です。
特に新しい従業員に対しては業務の流れや使用する機器についてしっかりと教育することが大切です。
トレーニングを通じて、従業員は作業の手順を理解し、必要なスキルを習得することができます。
これにより、自信を持って業務に取り組むことができ、ミスの発生を減少させることができるのです。
また、定期的なスキルアップトレーニングを実施することも効果的です。
業務の進化に伴い、新しい技術や方法が導入されることがあります。
従業員が最新の情報を持っていることは、作業効率の向上につながります。
例えば、ピッキング用の新しいソフトウェアや機器についてのトレーニングを行うことで、業務の精度を高めることができます。
さらに、ピッキング作業においては、チームでの作業が重要です。
チーム全体でのコミュニケーションを促進するためのトレーニングも役立ちます。
お互いの役割を理解し、協力し合うことで、ミスを未然に防ぐことができるだけでなく、業務全体の効率も向上します。
このように、作業効率化のためのトレーニングは、ミス防止のための重要な要素と言えるでしょう。
ピッキングミス防止テクニックその3 正確なデータ管理
データ管理の正確性は、ピッキング作業におけるミス防止において非常に重要です。
まず、商品の情報や在庫状況を正確に把握するためには、データベースの整備が必須です。
商品の種類や数量、ロケーションなどの情報を正確に入力し、常に最新の状態に保つことで、従業員は必要な情報を迅速に取得できます。
これにより、誤った商品をピッキングするリスクを大幅に減少させることができます。
次に、データの更新作業も重要です。
入荷や出荷が行われるたびに、在庫データを即座に更新することで、リアルタイムでの在庫管理が可能になります。
特に、システムを自動化することで、人為的なエラーを減少させることができます。
例えば、バーコードスキャンを利用した在庫管理システムを導入することで、手動での入力ミスを防ぐことができます。
データ管理の透明性も重要です。
従業員がデータにアクセスできる環境を整えることで、問題の早期発見が可能になります。
また、データの整合性を確認するための定期的な監査を行うことも効果的です。
これにより、データの不正確さを防ぎ、ピッキング作業の精度を高めることができます。正確なデータ管理は、業務の信頼性を高めるために欠かせない要素です。
ピッキングミス防止テクニックその4 作業環境の最適化
ピッキング作業の効率と精度を向上させるためには、作業環境の最適化が不可欠。
まず、倉庫内のレイアウトを見直し、商品の配置を最適化することが重要です。
よく出荷される商品を手に取りやすい場所に配置することで、ピッキングのスピードを向上させることができます。
適切な動線を確保することで、従業員の移動時間を減少させ、効率的な作業が実現します。
また、作業環境の安全性も重要です。
倉庫内が整理整頓されていることは、従業員がストレスなく作業を行うための基本です。
障害物がない清潔な環境を維持することで、転倒や事故のリスクを減少させることができます。
さらに、適切な照明を確保することで、作業のしやすさが向上し、ミスを防ぐことができます。
作業者の身体的負担を軽減するための工夫も大切です。ピッキング作業は体力を必要とするため、エルゴノミクスに基づいた機器や作業方法を導入することで、従業員の疲労を軽減します。
例えば、適切な高さの棚や、軽量な運搬具を使用することで、作業効率を向上させることが可能です。
作業環境の最適化は、従業員のモチベーションを高め、ミスを防ぐための大きな要素となります。
ピッキングミス防止テクニックその5 定期的な品質チェック
ピッキング作業におけるミスを防ぐためには、定期的な品質チェックが不可欠です。
作業後にピッキングした商品の確認を行うことで、誤ピッキングや数量ミスを早期に発見できます。
この確認作業はシステムで管理されるデータと実際の商品の一致を確認することを目的としています。
これにより、問題が発生した場合には、即座に対処することが可能です。
また、定期的な品質チェックは、従業員の意識向上にもつながります。
チェック作業を通じて、従業員は自分の作業に対する責任感を持つようになり、ミスを減少させることができます。
さらに、品質チェックの結果をフィードバックすることで、改善点を明確にし、業務の効率化につなげることができます。
最後に、品質チェックのプロセスを標準化することも重要です。
明確な基準を設け、誰もが同じ方法でチェックを行えるようにすることで、一貫性のある品質管理が実現します。
これにより、組織全体でのミス防止の意識が高まり、結果として業務の品質が向上します。
定期的な品質チェックは、ピッキング作業の精度を向上させるための重要な手段と言えるでしょう。
コメント